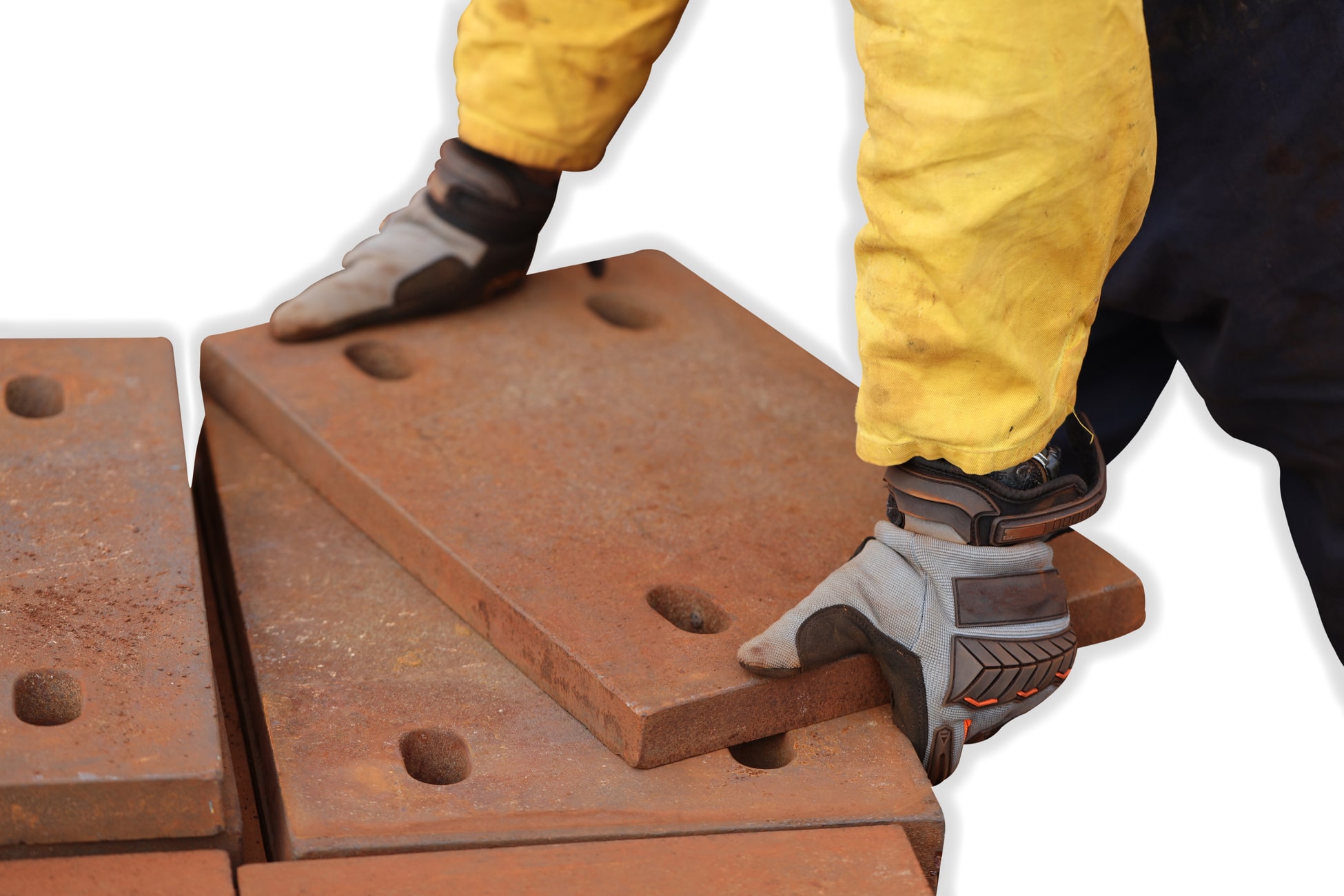
The Most Frequently Asked Questions on Manual Handling & Health & Safety
Set out below are the questions most often asked of Alastair Bromhead and his trainers by people who haven’t completed one of their training courses.
What should be taken into consideration when assessing manual handling risks?
Around 40 factors can contribute to the risk in a manual handling operation. Many handlers focus on the weight of the item, but risks can be increased due to task parameters (such as bending, twisting and reaching), individual capability, load (ease of grip, predictability and bulk) and the working environment (lighting, temperature and slippery floors).
Your risk assessment should decide on the significance of such factors and how the remedial action will reduce the level of risk. The prioritisation of solutions should be based on the hierarchy of control: eliminate when possible, mechanise, use manual handling aids and then rely on people measures such as training.
Alistair Bromhead Ltd provides courses and consultancy to help with risk assessments as well as training programmes to ensure staff are aware of risk and how to mitigate it. You can also find guidance from the Health and Safety Executive (HSE), which provides the Manual Handling Assessments Charts, a tool to help assess risks in lifting, lowering and carrying by individuals or teams. Guidance for other types of manual handling is issued in the form of leaflets.
What is the heaviest weight someone should be expected to lift at work?
This is not specified in the health and safety regulations, but managers and supervisors are expected to make such judgements based on ergonomic factors such as the task to be completed together with the working environment and the individual or team members concerned. You have to fit the job to the people.
Such decisions follow accurate risk assessments and are necessarily linked to them. Even someone with years of experience could not be confident of making the right decisions without them.
Are manual handling risks different for teams and individual handlers?
Some of the risks are the same, but additional factors need to be considered for teams. For example, they need to be able to hear each other speaking, so a noisy environment is particularly risky. If one member sees a potential hazard, or is in trouble, and cannot alert the others, they could all be in danger. They need to have enough space in which to manoeuvre together as well.
They all also need to have a good grip on the item, so consideration should be given to whether any handling aids are required for heavy items which are small or difficult to hold. Care should be taken to secure items on a stretcher or in a sling.
What will a good manual handling course cover?
The best manual handling courses are those that are tailored to the specific situation. For manual handling operatives and supervisors, the minimum will be to give delegates an awareness of the risks and the serious consequences that can arise from poor handling techniques, followed by presentation and demonstration of how to carry out their tasks safely, with and without appropriate handling aids. They should always include practical exercises to ensure that trainees can put the advice into practice.
Alistair Bromhead Ltd offers highly respected courses that cover all this and more. Programmes with recognised qualifications to train in-house trainers to provide courses for new recruits and to keep staff up to date on ergonomic developments are also popular. Contact us for more information on our range of courses.